Features | |
Materail | Sealing member:NBR,HNBR,ACM,EPDM,VMQ,PTFE,SBR,FKM,PU |
Spring:SWP,SUS | |
Metal case:Carbon steel | |
Color | Black,red,yellow,blue,orange,brown,purple,etc |
Availability | OEM,ODM |
Type | Serrated,Grooved, Corrugated,flat,ring,others as customer’s requirement |
Certification | ISO9001,TS16949,SGS |
Application | Car suspension, automobile engine,hydraulic system,air pressure system,Etc. |
item | value |
Warranty | 1YEAR |
Place of Origin | China |
Zhejiang | |
Brand Name | Max |
Density | 6.4-6.9 g/cm3 after steam oxidation |
Material | Fe-C-Cu Powder |
Surface treatmen | Steam oxidation, 2 hours, Fe3O4: 0.004-0.005mm, degree of oxidation 2-4% |
Service | OEM ODM |
Density | 6.4-6.9 g/cm3 after steam oxidation |
Type | DRILLING, Milling, Turning |
Model Number: | Custom-made Service |
Product name: | Powder Metal Sintered Part for Shock Absorber |
Process | Sintering+ Cnc |
Application | Shock Absorber |
Unspecified | ISO 2768 - m / H14, h14, +- IT14/2 |
Our Advantages | 1. More than current 3000 moulds ,save your mold cost 2. ISO/TS 16949:2009 certificate 3.Competitive price 4.Strictly quality control capacity of APQP,FEMA,MSA,PPAP,SPC |
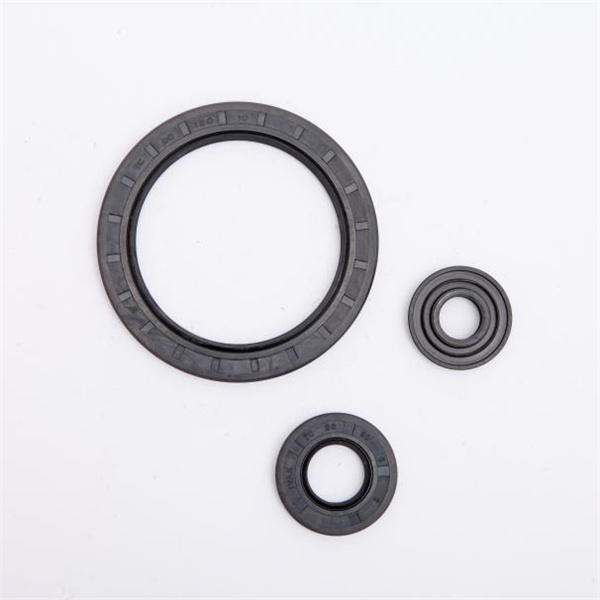
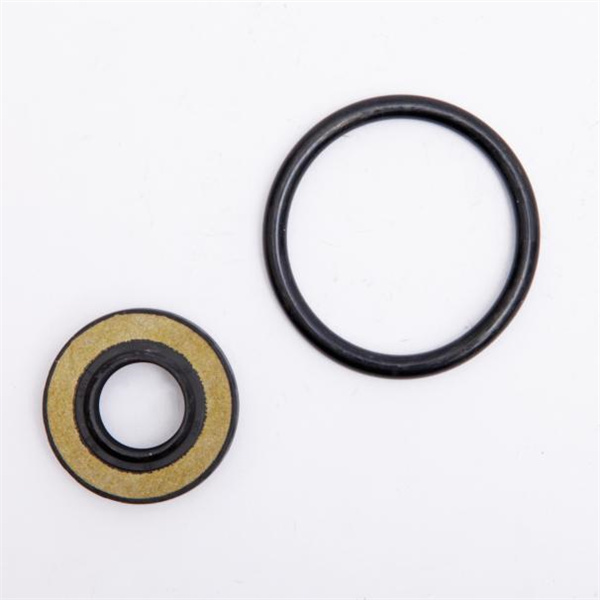
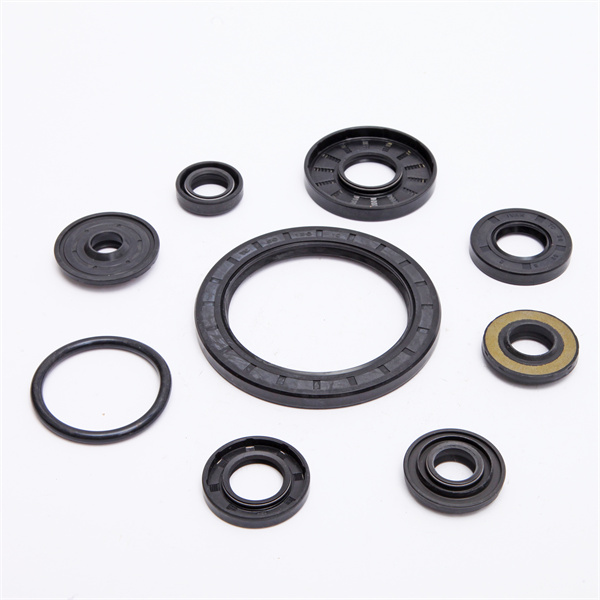
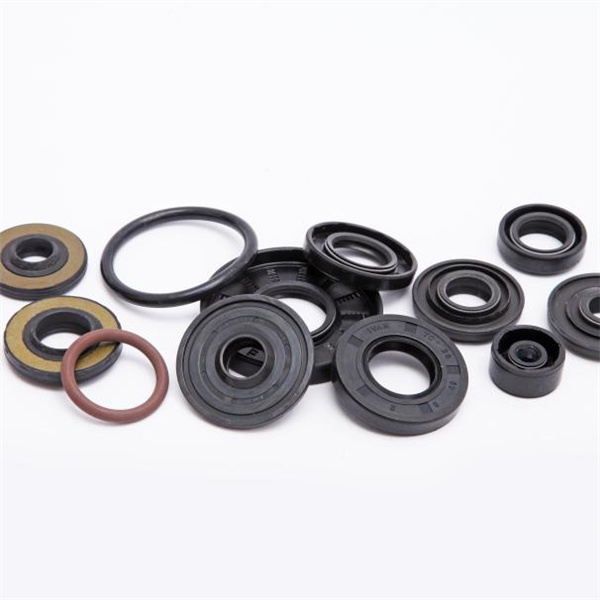
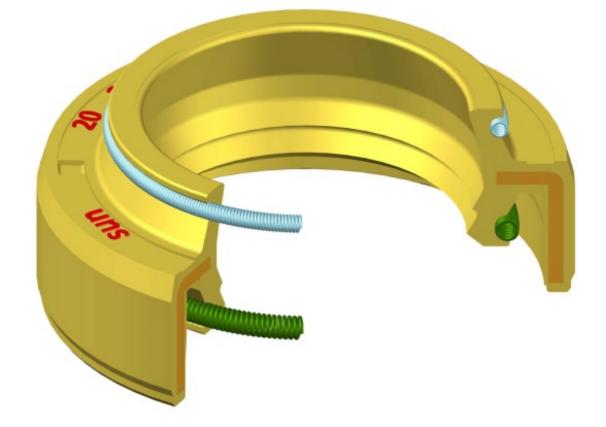
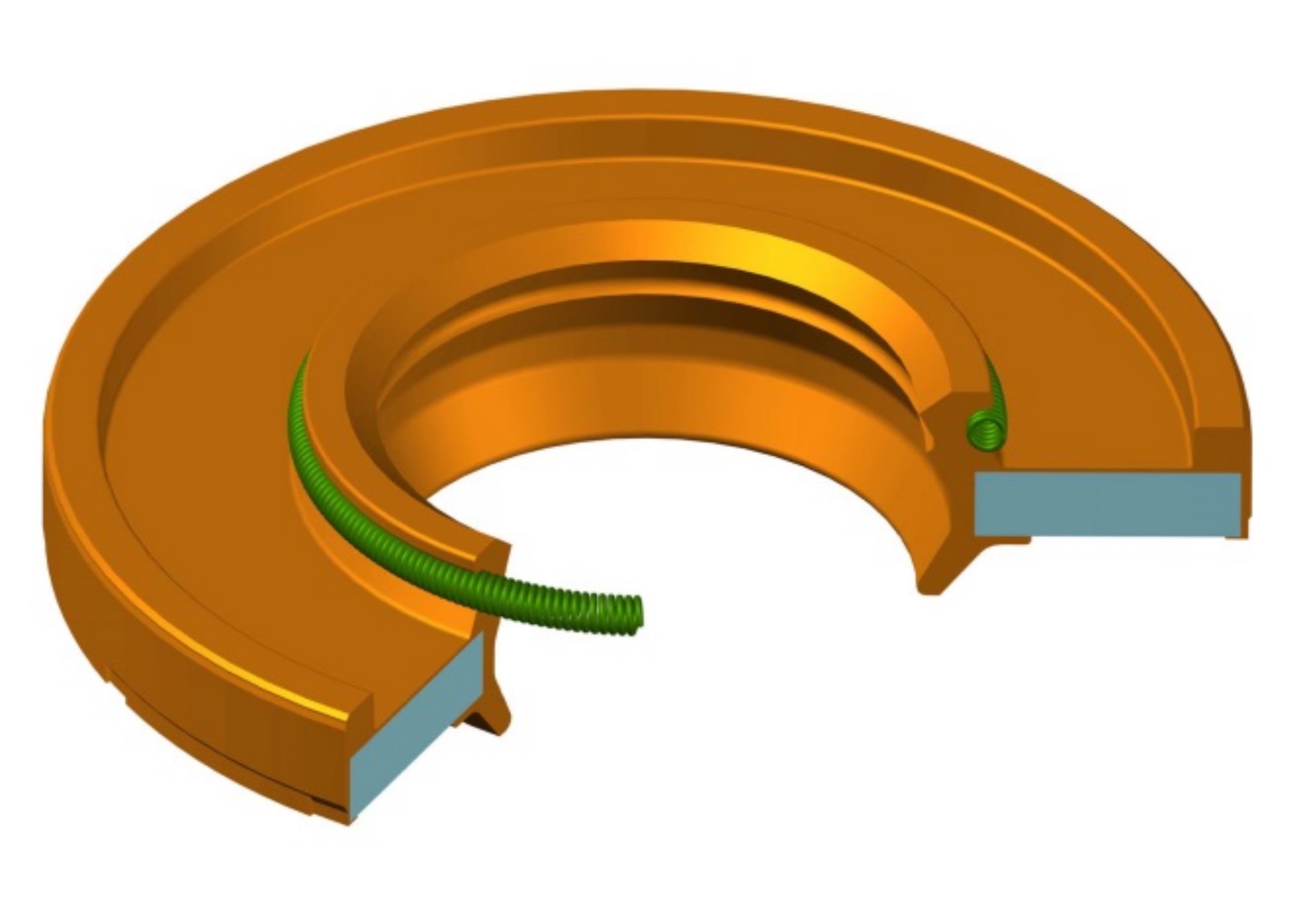
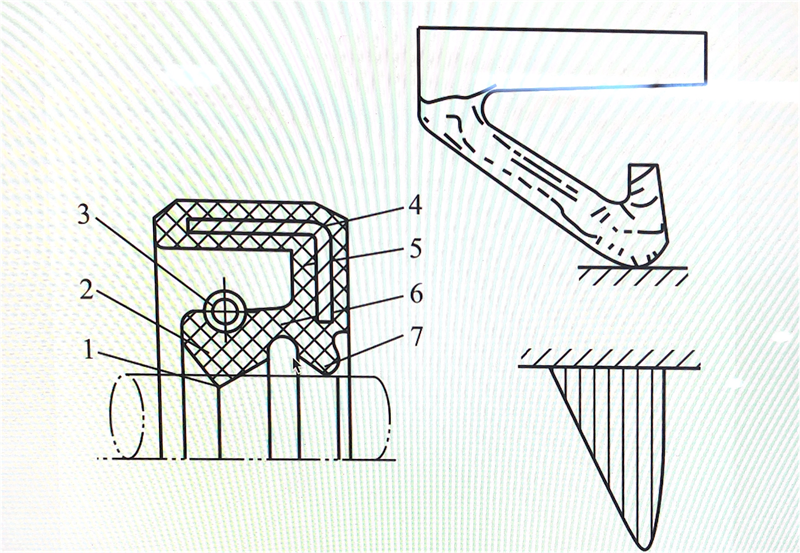
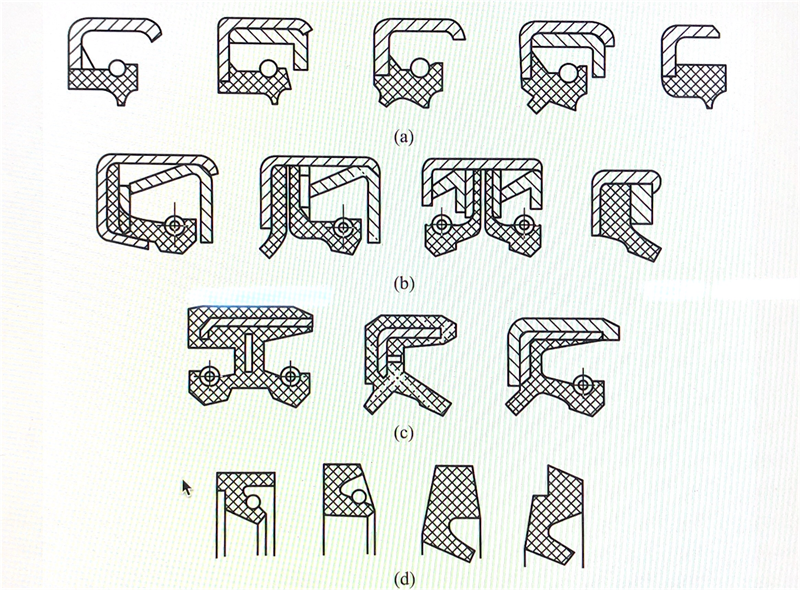
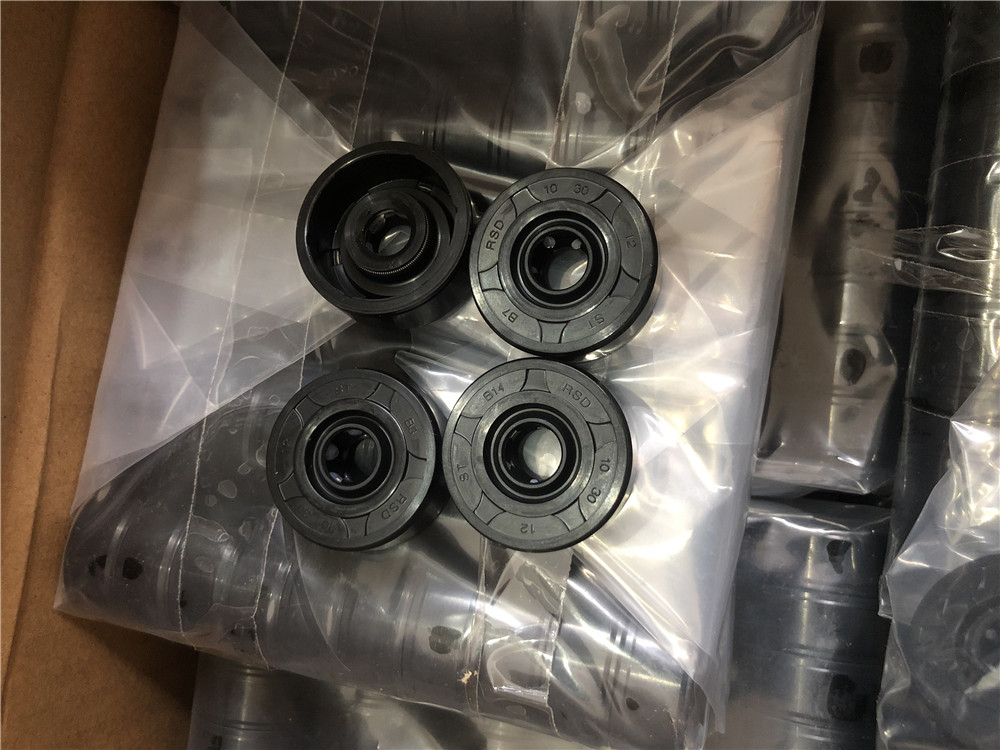
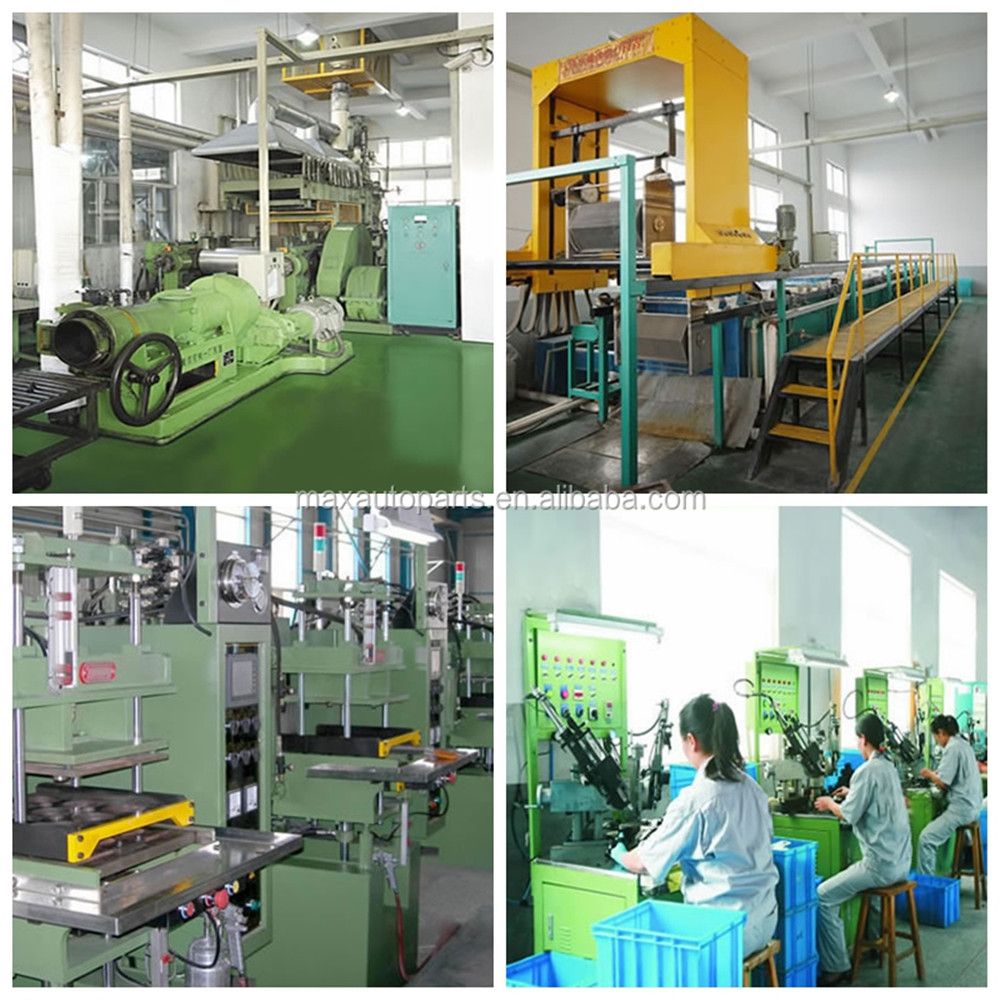
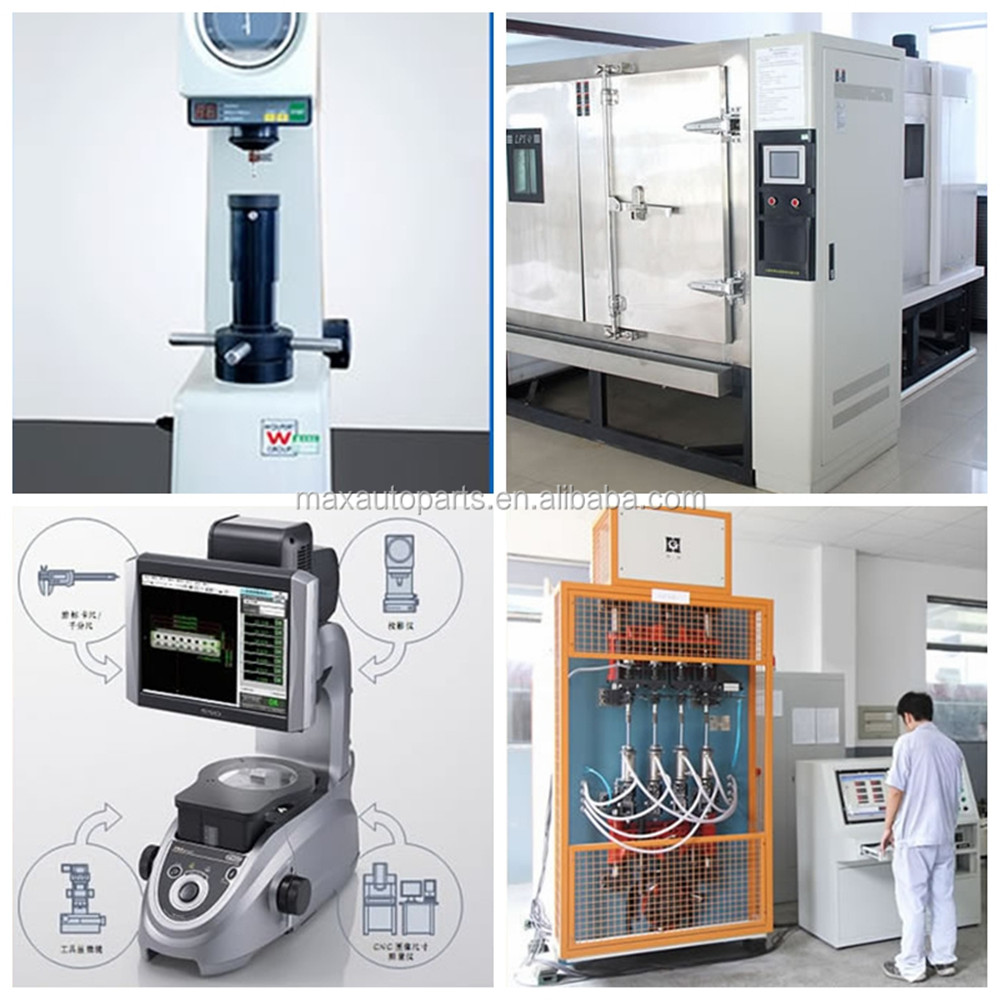